You’re in good company!
Machine Operation Apps: your benefits
Shorter response times
Tasks get assigned to the right person at the right time based on configurable business rules. This skill-based distribution reduces response times drastically.
Clear and consistent reporting
All machine operations workflows provide detailed information for precise issue reporting such as Missing material, Amount: 50, Type: Broken shafts, and Charge: 2364.
Prevent multiple people chasing the same issue
Real-time insights enable proactive issue resolution and process optimization, driving continuous improvement.
Fully integrated digital environment
All machine operations Connected Worker Apps work seamlessly together and integrate with existing machines and systems (ERP, MES and more).
A better way to operate machines
Our machine operations apps are completely adaptable to your specific processes. The Workerbase solution can be fully integrated into your existing IT infrastructure whether you`re working on-premise or in the cloud.
Machine alarms
You can start using our software within a few days, without impacting your production environment. No downtime. Instant value.
Machine changeovers
Walk teams through processes with customizable checklists. Keep track of critical steps and reduce mistakes. Improve first pass yield and maintain industry standards effortlessly.
OEE data collection
Collect machine and quality data directly from the shopfloor. Using customizable data input forms for smartwatches and smartphones, operators can efficiently feed back error codes and other missing data points from their personal device.
Andon support calls
Allow operators to efficienctly send Andon request to shorten reaction times and remove bottlenecks. Popular use cases include monitoring machine downtimes, creating material requests, and calling for support.
Non-conformities reporting
Identify non-conformities early on and notify the relevant people in real-time using emails or smartphone notifications.
…and more!
Use the Workerbase platform as a blank canvas to configure any workflow you need with complete flexibility.
Example workflow
The workerbase system is a fully configurable digital platform that can be meet you individual requirements. This is what a typical deployment process looks like.
Step 01
Connect your machines
The Workerbase connector framework allows you to connect any kind of machine or system. Whether you want to connect to the machine’s PLC controller directly, use an IOT gateway or send alarms by email or out of your MES system, we support all types of connection mechanisms and protocols. Connections are bi-directional, so as long as there’s an interface, you can send acknowledgements or repair results to your existing systems.
Step 02
Send real-time alerts to your operators
Your workers are equipped with digital devices such as smartwatches or smartphones, and you start saving precious time from day one. Alert your operators in real-time on their personal smart devices and immediately initiate corrective actions. Each alert sent to your staff gets the problem solved quicker, thereby reducing machine downtime.
Step 03
Predict machine failures
There are many ways to predict machine disruptions. Workerbase can enhance the quality of those prediction by feeding you additional data from human operations. Tracking the time and nature of repair on top of the basic failure data significantly increases the accuracy of your predictions. By monitoring critical machine parameters and adding human generated data, you can prevent machine failure by alerting frontline staff even before disruptions occur.
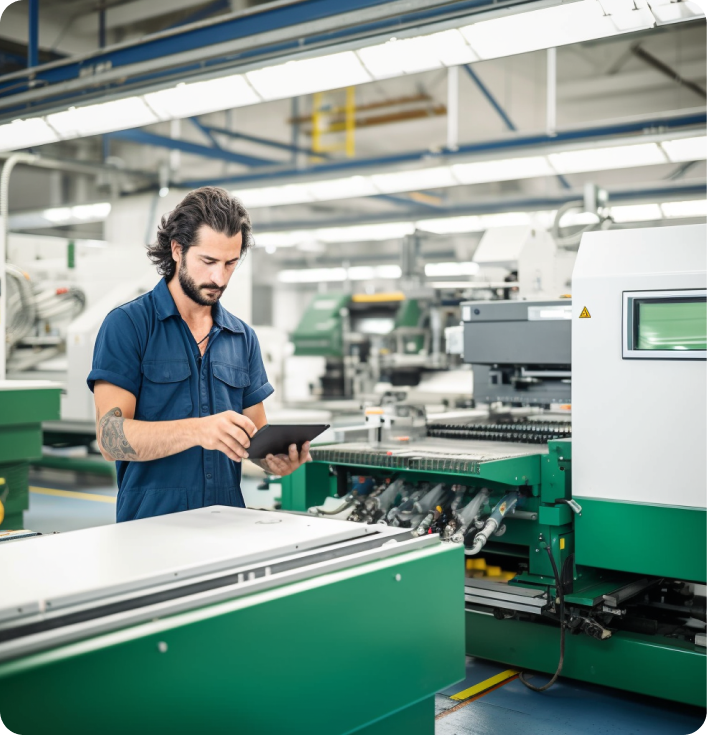
Connected Worker app bundle designed for machine operations
Get in touch with us
Ready to dive into Workerbase’s Connected Worker platform? Receive a personalized demo tailored to your challenges. Schedule a call now!
- Connect workers with industrial grade smart devices
- Integrate your ERP and MES systems for a holistic view
- Track progress and visualize work as it happens