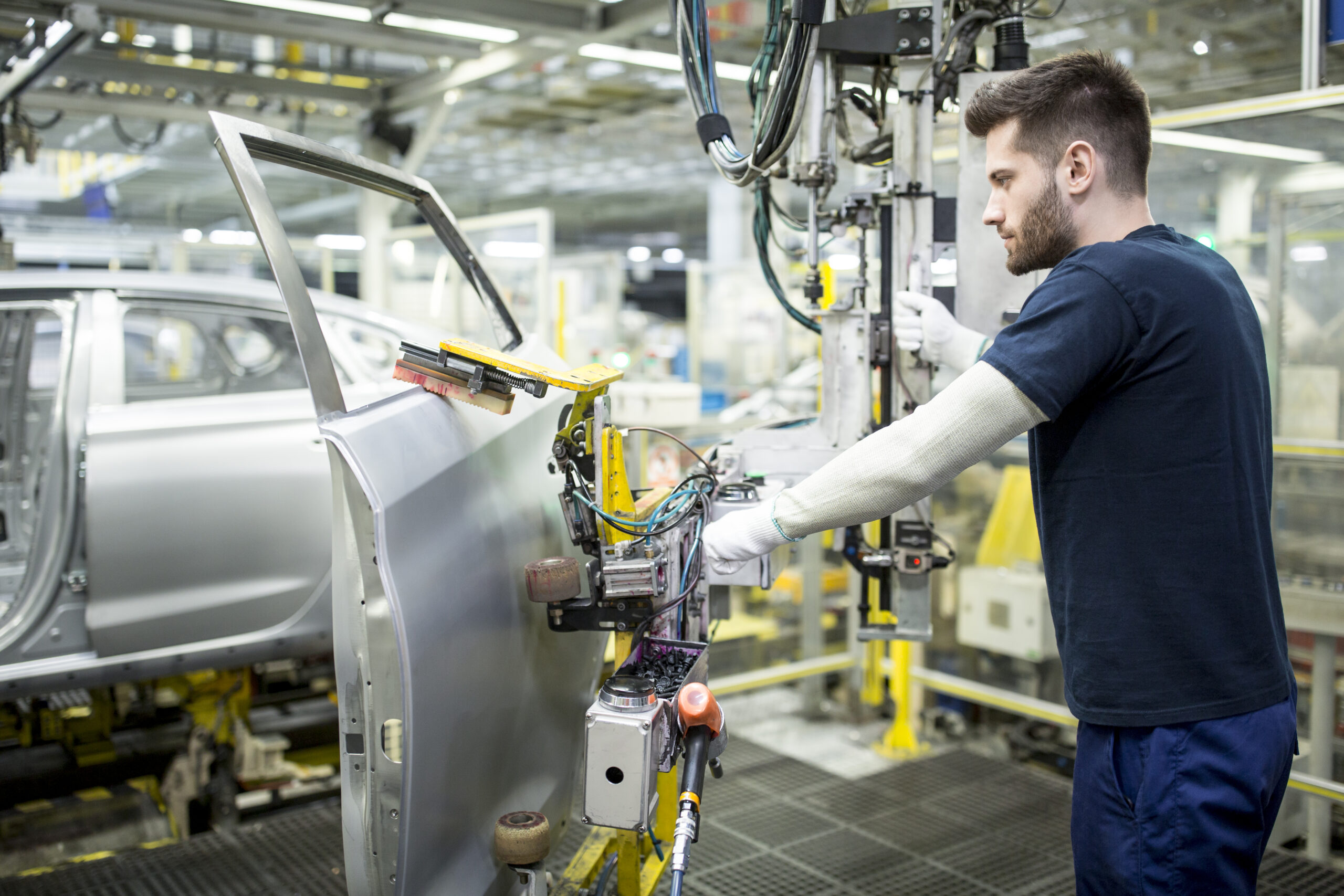
Upgrade your Automotive production: Prevent belt downtime and enable inline repairs
Apart from digitally coordinating inline repairs, you can also prevent assembly belt stops by smartly using your process data to orchestrate preventive actions.
Solve the hard challenges in Automotive assembly that cannot be solved by other systems
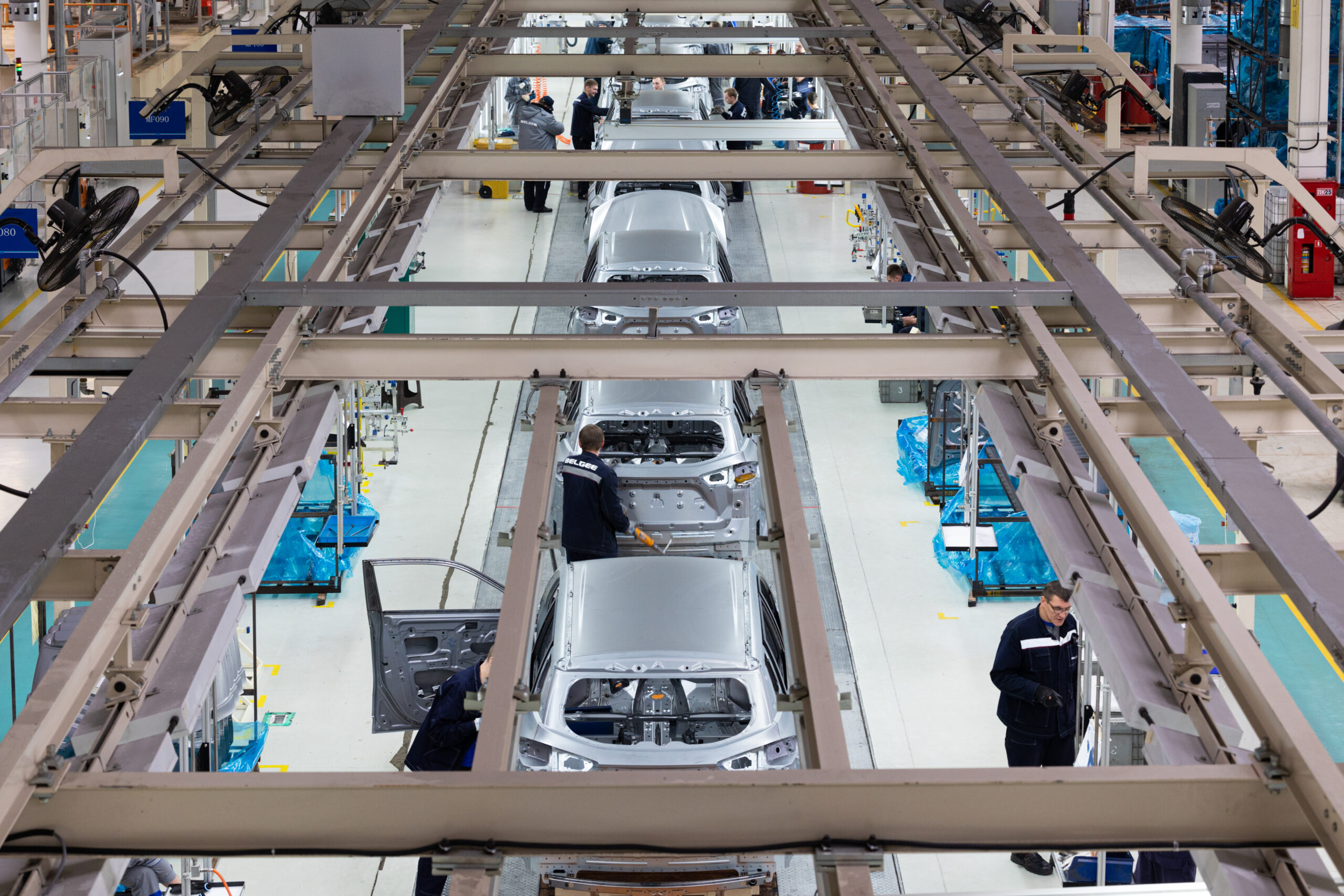
Automotive IT systems are the most advanced issues?
Many systems in the Automotive domain are highly specialized to squeeze every second out of the production process. Yet there are plenty of white spots that are only covered by inferior technology which causes inefficiencies, even in the main assembly belt.
✖️ Doing line balancing with Excel sheets? Too commplicated.
✖️ Managing rework in your ERP? Too messy.
✖️ Running line support using pull ropes? Too limiting.
You don’t have to settle for this – start changing today!
Workerbase offers several solutions that work out of the box. If your problem is not covered we also have a unique approach to manufacturing consulting to help you boost your productivity.
Implementing the Workerbase Connected Worker Platform takes less than 4 weeks
Finding solutions to some of your long standing problems may seem complicated. We have compiled our expertise into ready to use applications that allow you to get started in a short time.
Rework coordination
Automatically coordinate rework based on all essential criteria such as bay capacity, worker skills and sparepart availability. Workerbase ensures your rework processes run smoothly all the way through.
Line support and inline repairs
Reduce line downtime by speeding up support and inline repair services. Utilize the data collected to take preventive measures.
Line balancing
Reduce tact time by mapping assembly processes across stations and visualize actual performance in real time for each product.
Logistics
Automatically coordinate deliveries to maximize belt performance and increase delivery efficiency with digital coordinated milk runs.
Implementing the Workerbase Connected Worker Platform takes less than 4 weeks
Finding solutions to some of your long standing problems may seem complicated. We have compiled our expertise into ready to use applications that allow you to get started in a short time.