Seamless, error-free production with our manufacturing assembly software
You’re in good company!
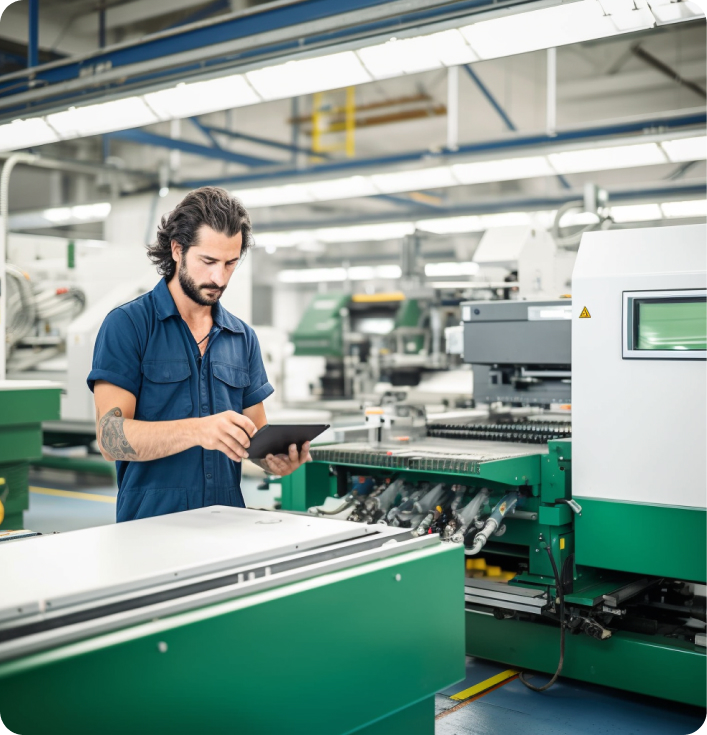
Flawless assembly processes with Connected Worker apps
Bye-bye cumbersome paper instructions. Hello agile digital assembly workflows.
Our Connected Worker apps are flexible enough to suit your specific manufacturing assembly software needs and work harmoniously together in a one-stop-shop solution. Whether you start with a single app for one assembly work station or configure multiple workflows for all assembly lines, we get you up and running swiftly so you can immediately benefit from digital assembly workflows
Work Instructions
Ensure Precision with step-by-step workflows that guarantee accurate assembly, reduce errors and minimize rework.
Training
Enable new operators to onboard fast and seasoned operations to adapt quickly. Make complex assembly processes easy to ensure consistent output.
Audit checklists
Conduct real-time quality assurance audits to verify assembly correctness and instantly identify deviations.
Continuous Improvement
Monitor and interpret audit data to uncover actionable insights you can implement as process enhancements to optimize your assembly line.
Traceability
Achieve complete transparency by digitally tracking components throughout the assembly process, ensuring accountability and compliance.
…and more!
Use the Workerbase platform as a blank canvas to configure
any workflow you need with complete flexibility.
What You Get from Our Assembly apps
Efficiency Boost
Significant reduction in assembly errors and rework result in enhanced productivity and reduced operational costs.
Data-Driven Decision-Making
Workload between machine operators is automatically distributed. Notifications are only sent to relevant people.
Seamless Compliance
Ensure adherence to quality standards and regulatory requirements, mitigating risks and safeguarding your brand reputation.
Accelerated Onboarding
Speed up new employee onboarding and skill development with guided work instructions, thereby boosting the knowledge, confidence and motivation of your saff.
Quick fix
Swiftly identify and address any irregularities, ensuring product integrity.
5S Checklists
Maintain an organized and efficient assembly environment through regular 5S checklists.
Your factory. Without disruptions.
Increase throughput
Reduce quality costs
Improve productivity
Get in touch with us
Ready to dive into Workerbase’s Connected Worker platform? Receive a personalized demo tailored to your challenges. Schedule a call now!
- Connect workers with industrial grade smart devices
- Integrate your ERP and MES systems for a holistic view
- Track progress and visualize work as it happens