Increase order fulfillment, reduce lead times and improve inventory accuracy
You’re in good company!
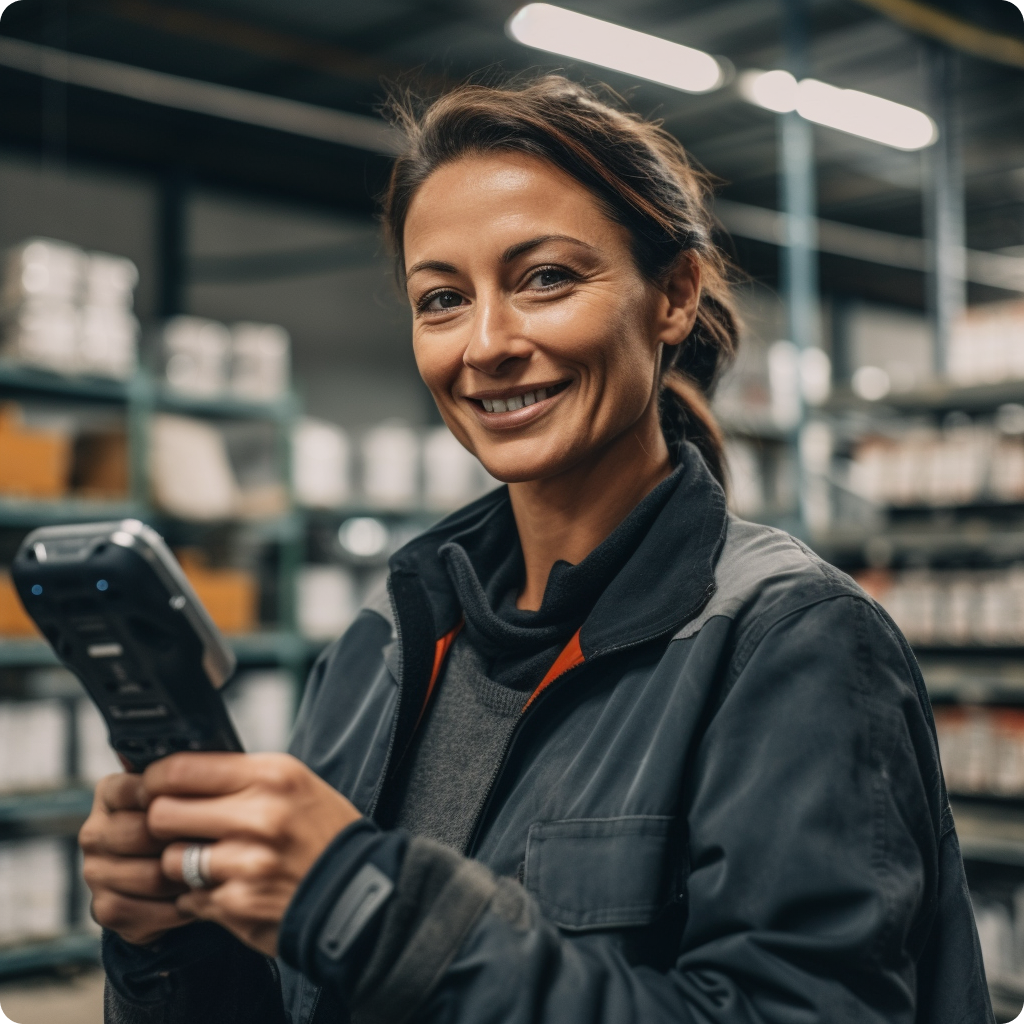
Efficient intralogistics procedures with Connected Worker apps
Prevent disruptions caused by material shortages and delays
Designed for maximum flexibility, our intralogistics software can be easily configured to meet specific your needs, reducing bottlenecks, improving inventory accuracy, and enhancing operational efficiency across the factory floor.
Material Replenishment
Ensure timely availability of materials by utilizing real-time material calls to request replenishment when needed
Digital Kanban
Digitize your Kanban process, ensuring automated material replenishment and real-time visibility into material usage
Support Call
Enable operators to request immediate support, ensuring efficient issue resolution and minimal production interruptions.
Picking & Kitting
Streamline picking and kitting processes with guided instructions, minimizing errors and optimizing productivity.
Packing instructions
Ensure accurate assembly and packaging of materials for accurate order fulfillment
Forklift Coordination
Coordinate forklift operations in real-time, optimizing routes, and minimizing wait times.
Training
Enable new operators to onboard fast and seasoned operations to adapt quickly. Make complex assembly processes easy to ensure consistent output.
What you get from our intralogistics software
Enhanced Material Availability
Real-time replenishment and digital Kanban ensure materials are readily available on a just in time basis, minimizing delays and optimizing production schedules.
Efficient Resource Utilization
Streamlined forklift coordination and task execution lead to optimized resource allocation and reduced idle times.
Accelerated Task Completion
Picking & Kitting guidance ensures tasks are executed efficiently, promoting overall workflow speed and reducing non-conformance costs
Minimized Disruptions
Real-time support calls and guided task execution contribute to a seamless and uninterrupted intralogistics process.
Your factory. Without disruptions.
Increase throughput
Reduce quality costs
Improve productivity
Get in touch with us
Ready to dive into Workerbase’s i? Receive a personalized demo tailored to your challenges. Schedule a call now!
- Connect workers with industrial grade smart devices
- Integrate your ERP and MES systems for a holistic view
- Track progress and visualize work as it happens