Ensure product quality with digital workflows
You’re in good company!
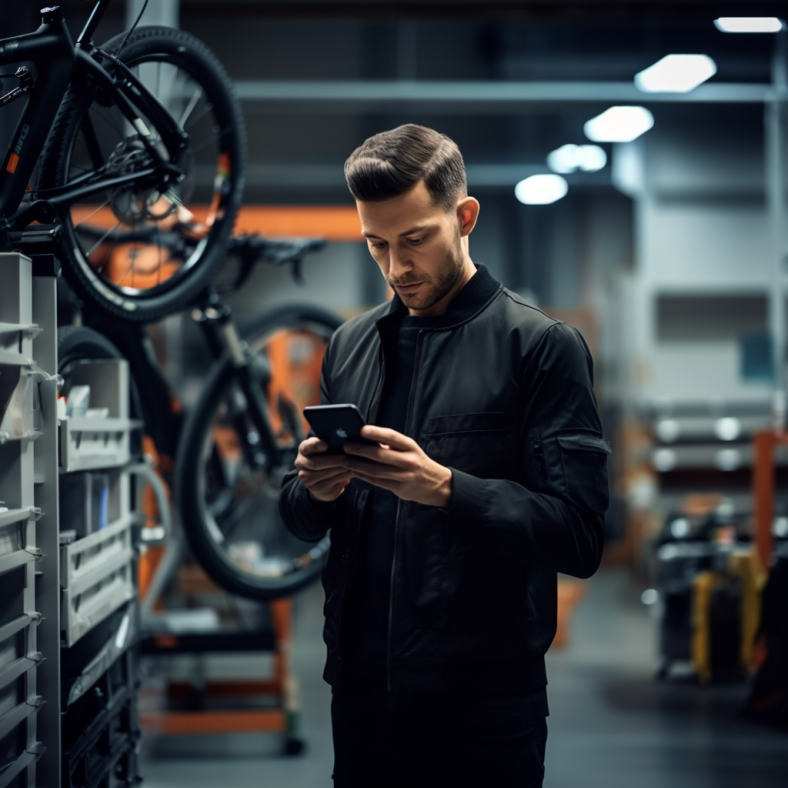
Precise Quality Control with Connected Worker apps
Elevate your quality control processes to ensure your products exceed customer expectations and stand out among the competition.
Minimize waste and maximize productivity
Our Connected Worker apps are flexible enough to suit your specific manufacturing quality software needs and work harmoniously together in a one-stop-shop solution. Whether you start with a single app for one quality work station or configure multiple workflows for all quality processes, we get you up and running swiftly so you can immediately benefit from digital quality workflows.
Quality Approval
Ensure flawless approval processes, reducing bottlenecks and enhancing overall production efficiency.
Continuous Improvement
Monitor and interpret audit data to uncover actionable insights you can implement as process enhancements to optimize your assembly line.
Issue Resolution
Promptly detect and address any quality deviations, upholding your commitment to excellence.
Inline Service Coordination
Facilitate real-time collaboration between quality control and service teams to address issues without delay.
Audit checklists
Conduct real-time quality assurance audits to verify assembly correctness and instantly identify deviations.
Traceability
Achieve complete transparency by digitally tracking components throughout the assembly process, ensuring accountability and compliance.
Rework
Streamline rework procedures with guided instructions, ensuring faulty products are swiftly brought up to standard.
Non-conformities reporting
Identify non-conformities early on and notify the relevant people in real-time using emails or smartphone notifications.
What you get from our quality apps
Unparalleled Quality
Ensure product excellence through real-time quality control, enhancing customer satisfaction and brand reputation.
Proactive Issue Resolution
Real-time auditing and reporting enable swift identification and resolution of quality deviations, minimizing waste and rework.
Enhanced Traceability
Achieve end-to-end transparency, safeguarding product integrity and ensuring compliance with regulatory standards.
Operational Efficiency
Streamline quality processes and reduce production disruptions for a more agile and competitive manufacturing operation.
Your factory. Without disruptions.
Increase throughput
Reduce quality costs
Improve productivity
Get in touch with us
Ready to dive into Workerbase’s Connected Worker platform? Receive a personalized demo tailored to your challenges. Schedule a call now!
- Connect workers with industrial grade smart devices
- Integrate your ERP and MES systems for a holistic view
- Track progress and visualize work as it happens