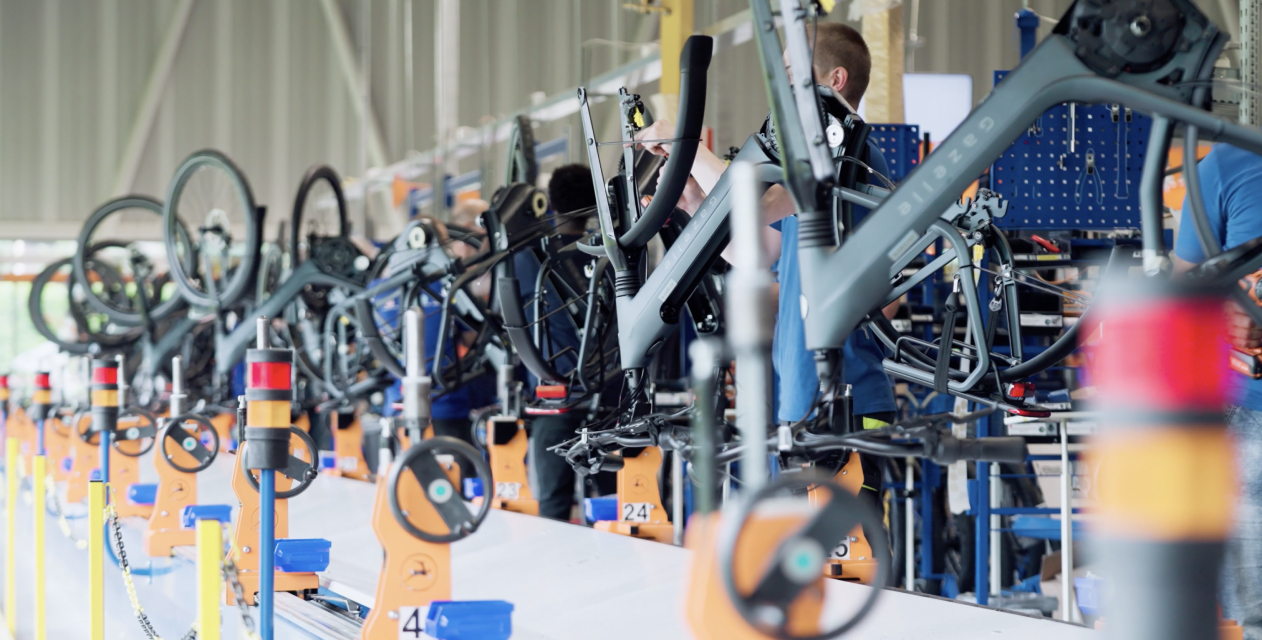
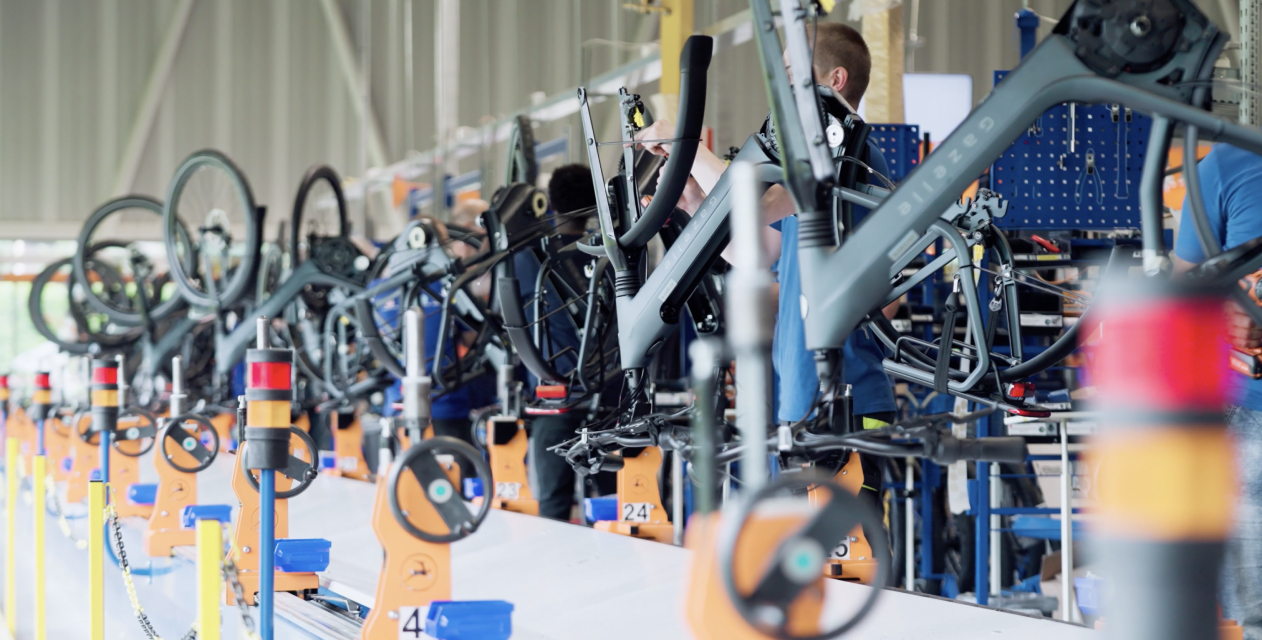
About Gazelle
Royal Dutch Gazelle has been a bicycle manufacturer for over 130 years and is the leading bicycle manufacturer in the Netherlands. As a subsidiary of PON group, they produce a variety of bikes including e-bikes and are a premium dutch brand. Their factories assemble bikes along a belt driven system and produce around 300,000 bicycles a year.
Industry
Bicycle manufacturer
Company size
~750 Employees
Specialties
Known for it’s award winning designs and was recognized by the dutch royal family for their achievements. They officially bear the title of Royal Dutch Gazelle.
The Challenge
Gazelle approached Workerbase with the goal of reducing the downtime of their assembly belt. The downtimes were not recorded in a central system and the root causes of belt stops were largely unknown. The continuous improvement team at Gazelle was facing several challenges:
- The assembly belt was stopped by simple push buttons and the reasons for stopping were unknown
- The support staff were not adequately prepared when responding to incidents because the root cause of the stoppage was only clear after they arrived at the station
- The duration of belt stoppages were not being recorded reliably, leading to a lack of transparency on the impact of the belt stoppages
- There was no easy way to tackle these challenges with traditional technology
The Solution
We helped Gazelle overcome their challenges by implementing our Digital Andon system for executing and recording belt stops. The solution now gives Gazelle full transparency:
-
- The belt is now stopped using the Workerbase Andon system installed on a tablet at each station of every line.
- The Andon system is directly connected to the belt PLC to stop and restart the line.
- All information for each bike on the assembly line was synchronized with SAP, providing clear visibility of which specific bike is being produced at each station.
- When an operators are now prompted to record the root cause when triggering a belt stoppage, which is verified by the support staff after resolution ensuring data quality.
- Belt support staff are equipped with Smartwatches to receive belt stop notifications in real-time.
- Data collected during this process is centralized into one analytics tool that is used to identify trends in the root causes of the belt stops. All the relevant contextual information is also captured such as which station executed the stop, which bike was produced at that station, and what the stop reason was.
The Results
With the added transparency, Gazelle was able to analyze the root causes of their belt stops and take preventive action. From day one of implementing Workerbase, Gazelle was able to avoid a significant amount of line stops and produce more bikes every day. The solution amortized in less than 3 months.
Reduced Downtimes
The team was able to reduce production downtime by 35% by using real-time data to continuously improve the production process.
Increased throughput
The improvements in operations boosted throughput, with an extra 3,500 bikes being produced every year with no additional equipment or workers.
Continuous Improvement
Through collaboration with Workerbase, Gazelle is empowered to discover more areas for improvement using our platform.
Discover Why Industry Leaders Choose Workerbase
Workerbase’s Connected Worker platform offers manufacturers a one platform solution to the digitization and optimization of their operations.
Ready to dive into Workerbase’s Connected Worker platform? Receive a personalized demo.
- Empower workers with industrial grade smart devices and AI
- Integrate your ERP and MES systems onto one unified platform
- Leverage and analyze data from your entire manufacturing ecosystem