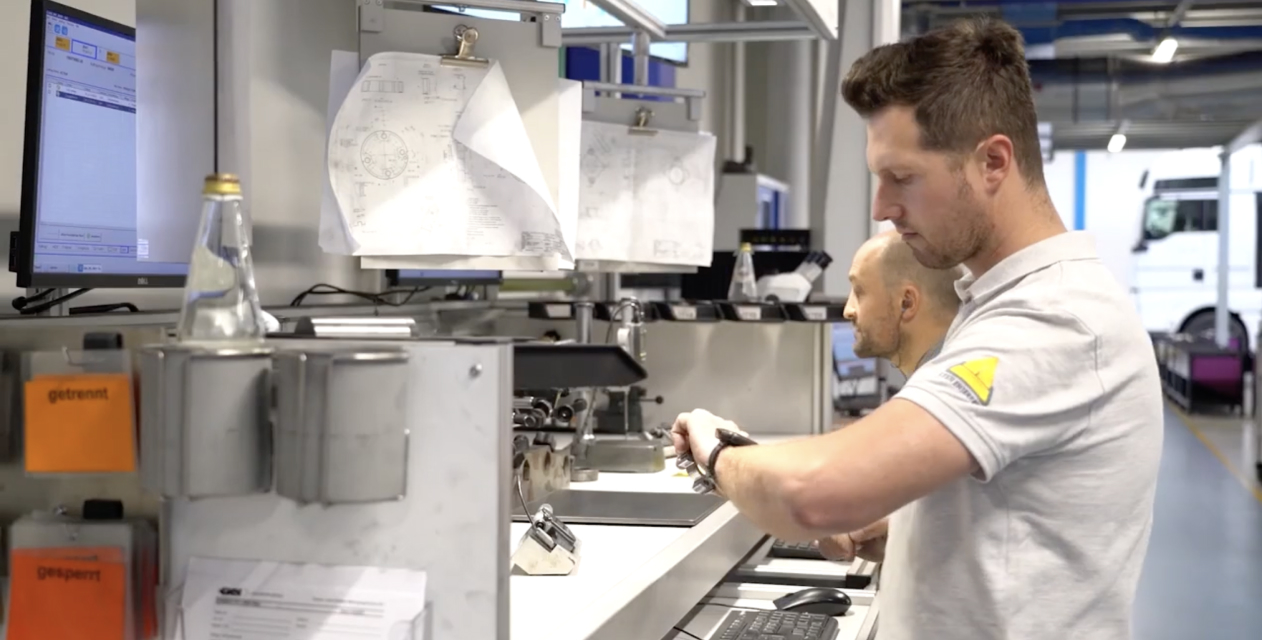
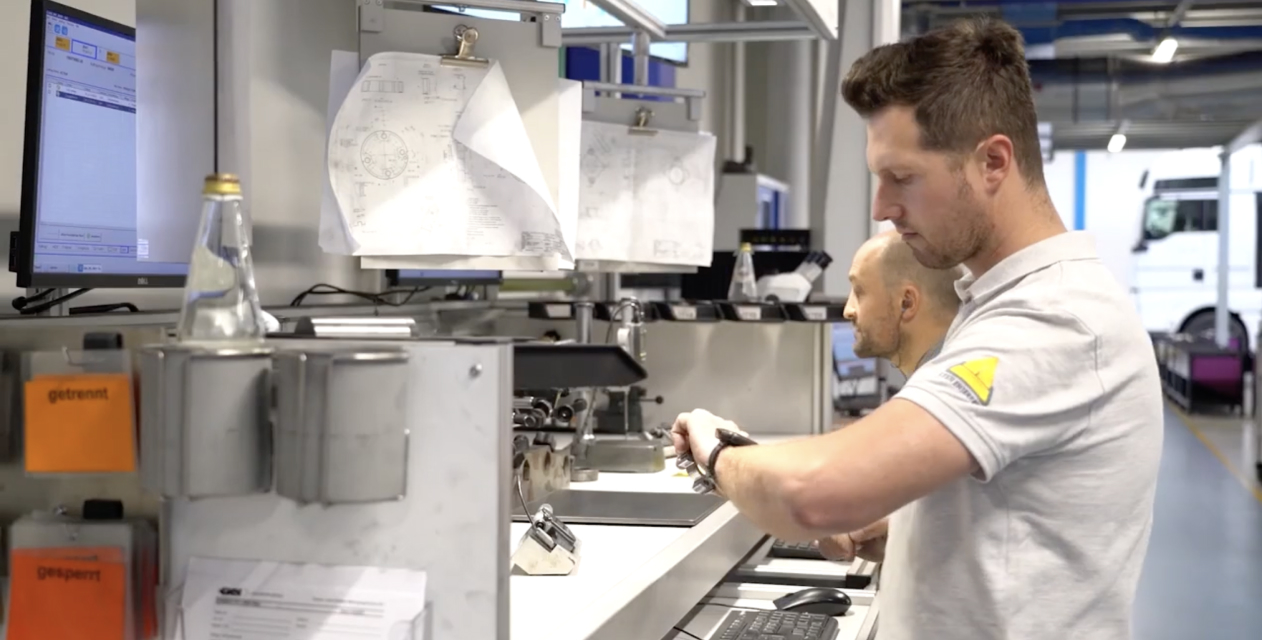
About GKN
GKN Powder Metallurgy is a global leader in metal powder production and in precision powder metal parts for the automotive and industrial sectors.
Metal powders are mixed and transported to forming stations where high pressure forming is used to bind the powder particles. After a heat treatment, the so called sintering process, the parts become solid and get transferred into post-processing (e.g. sizing, milling or drilling). GKN is increasing operational flexibility and worker productivity using Workerbase.
Industry
Sinter Metal Manufacturing
Company size
>5000 Employees
Specialties
The world’s leading manufacturer of precision powder metal products, sintered structural parts, porous products and filters, sub assemblies, soft magnetic components, and e-motor solutions.
The Challenge
In their day to day operations, GKN wanted to address several challenges to improve their overall operational effectiveness:
- Workers often needed to access several different databases to gather information leading to unnecessary downtime.
- Change-overs of equipment and material after each production cycle being slow and error prone, limiting flexibility to deal with small batch sizes.
- Improvement and optimization of workforce utilization, as workers weren’t redirected to support others during activity peaks.
The Solution
To address these issues, there were several different solutions implemented. At the outset of the implementation journey, frontline workers were equipped with smartwatches to allow for streamlined data access from anywhere and anytime.
Then, using our low-code custom workflow builder, team members at GKN were able to digitize their machine changeover process with workflows to streamlining notifications for production cycle status, informing workers to prepare the necessary source materials and more. Additionally, several prebuilt workflow apps were also applied to great effect such as inventory management, material traceability and material transport requests.
The Results
With the deployment of the Workerbase platform, GKN Powder Metallurgy was able to optimize and aim to continuously improve their shop floor operations. After adopting our platform, they are able to independently develop, test and implement new digital solutions on their own to meet their unique production needs.
Increased Throughput
Digital workflows mitigated downtimes from machine changeovers and stoppages. Skills based task delegation also optimally leveraged their workers to increase productivity.
Increased Flexibility
Assignment of tasks based off of machine data in real time allowed for faster reactions to changes in production and a leaner approach to material management.
Cost Savings
Due to better information access and better production cycle management, GKN was able make their production cycles leaner and reduced WIP inventory.
Discover Why Industry Leaders Choose
Workerbase
Workerbase’s Connected Worker platform offers manufacturers a one platform solution to the digitization and optimization of their operations.
Ready to dive into Workerbase’s Connected Worker platform? Receive a personalized demo.
- Empower workers with industrial grade smart devices and AI
- Integrate your ERP and MES systems onto one unified platform
- Leverage and analyze data from your entire manufacturing ecosystem