Material Replenishment
Frontline workers can report missing materials directly from their work station. All material is aligned with the current product and work step.
Frontline workers can easily select items and the quantity from the product's BOM list. The system assigns the material request to an available colleague via the automatic task coordination.
Automated replenishment impact on your bottom line
Reduced inventory levels
Enable just-in-time replenishment and eliminate excess stock—less tied-up capital, more efficient flow of materials.
Avoidance of waiting time and production delays
Deliver the right material to the right place at the right time—so production never stops for missing parts.
Increased Worker Productivity
Equip your team to act faster and with fewer errors—every task, every time.
Why use the Material Replenishment App?
How our Material Replenishment App streamlines your manufacturing operations
Existing Processes
- Error prone process of navigating through large material lists
- Time consuming method of seeking help (e.g. via phone or leaving the workplace)
- Missing knowledge about how often and why missing material is requested
With Workerbase
- All material lists are filtered for the current product and production step at each station
- Material replenishment request is automatically routed to the right person
- Detailed statistics about material requests enable reduction of inventory
Easy steps to implement Material Replenishment
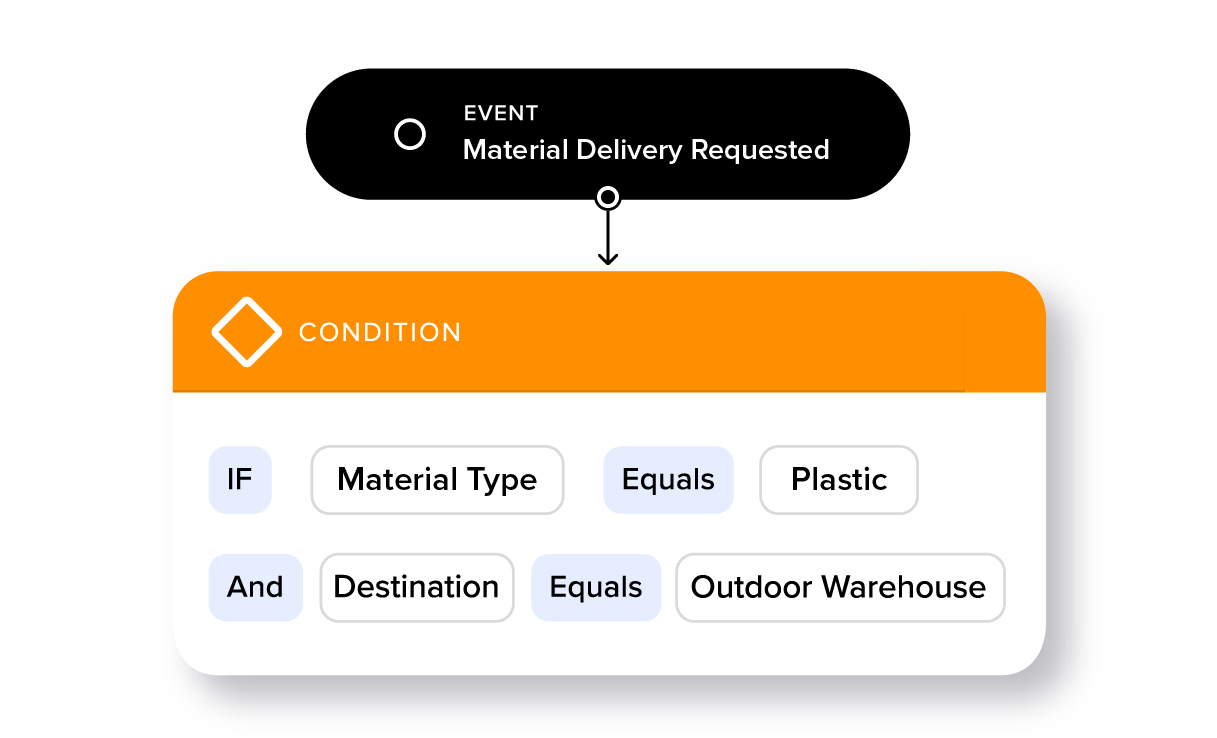
Define how material is delivered
Setup processes for how to handle replenishment:
- Based on averages
- Based on actual material consumption
- Based on manual requests
- Based on your custom logic using our low code editor
- Automatically create tasks for urgent deliveries or pool requests for regular milk runs.
Discover Why Industry Leaders Use Workerbase
We’d love to walk you through how our platform can solve your specific manufacturing and production challenges and deliver measurable results.
We’d also be happy to share more insights on how our platform tackles challenges such as:
- Information access and task related support for frontline workers
- Inflexible and siloed IT infrastructure, such as existing MES or ERPs
- Achieving data maturity from your entire manufacturing ecosystem