Manufacturing executives often ask themselves why their digital transformation initiatives aren’t delivering the expected results – despite significant investments in ERP and MES systems. The answer lies in a critical gap in the manufacturing IT stack: the lack of a comprehensive platform for human workers. This article explores how Connected Worker Platforms (CWPs) are filling this gap, delivering substantial returns, and transforming manufacturing operations.
The Limitations of Traditional Manufacturing IT Systems
While ERP and MES systems are foundational to manufacturing operations, they were designed with fundamentally different objectives than managing human-centric workflows. ERP systems excel at managing business transactions, financial data, and resource planning, but they struggle with the dynamic nature of shop floor operations. Their user interfaces are optimized for office workers entering structured data, not for operators working in dynamic production environments.
MES systems, on the other hand, are built to connect with machines, gather production data, and manage automated processes. However, they typically treat human workers as static resources rather than dynamic participants in the production process. This limitation becomes evident in several critical areas:
Real-time Adaptability
While MES systems can adjust machine schedules based on automated signals, they lack the capability to quickly adapt to human-driven changes. When a skilled worker identifies a quality issue or process improvement opportunity, the rigid structure of MES systems makes it difficult to capture and act on this information in real-time.
Worker Intelligence
MES systems excel at collecting data from sensors and automated equipment but struggle to incorporate human observations, decisions, and knowledge. A worker’s decision to adjust a process based on material variations or quality observations often goes unrecorded or is captured too late to be actionable.
Process Flexibility
Manufacturing processes often require human judgement and adaptation. While ERP systems can manage standardized processes and MES systems can control automated ones, neither is designed to handle the flexible, knowledge-based workflows that human workers execute. This leads to a significant gap in process documentation and optimization.
These limitations force manufacturers to create workarounds, typically in the form of standalone applications, spreadsheets, and paper-based systems. While these solutions may address immediate needs, they create data silos, compliance risks, and inefficiencies that ultimately undermine the benefits of core ERP and MES investments.
The Financial Promise of Connected Worker Platforms
The financial impact of implementing a Connected Worker Platform extends far beyond simple cost reduction. A mid-sized manufacturing facility typically sees a return on investment within 3-9 months, with benefits cascading across multiple operational areas. Take the example of a 500-worker facility: while the initial investment averages around €300,000, including platform licensing, implementation, and training, the annual benefits often exceed €2.5 million through IT cost reduction, productivity improvements, quality enhancements, and resource optimization.
These aren’t just theoretical numbers. The real impact becomes clear when examining IT maintenance costs alone. Many facilities maintain hundreds of small, unmanaged applications, each requiring separate maintenance and support. By consolidating these applications into a single platform, companies typically reduce their IT maintenance costs by €300,000-500,000 annually. Add to this a 70-90% reduction in new application development costs through no-code or low-code capabilities, and the financial case becomes compelling.
The Unique Challenge of Shadow IT Conversion
While many vendors offer Connected Worker Platforms, the critical challenge of converting existing shadow IT applications reveals significant differences in their capabilities. Most platforms focus primarily on digitizing documents and creating basic forms or checklists. While useful, this limited functionality addresses only a small portion of the shadow IT landscape in manufacturing.
The reality of manufacturing IT is far more complex. A typical factory maintains dozens if not hundreds of small applications that handle diverse workflows: from complex quality inspections and material tracking to specialized production planning tools and custom reporting solutions. Many of these applications involve sophisticated business logic, multi-step workflows, complex data handling, and intricate user interactions that go far beyond simple forms and checklists.
Why Traditional Connected Worker Platforms Fall Short
Most Connected Worker Platforms face several limitations when attempting to convert existing applications:
- Their form-based approach can only handle straightforward, linear processes. However, manufacturing workflows often involve complex branching logic, conditional processes, and dynamic data relationships that cannot be represented in simple form structures.
- Traditional platforms lack the ability to integrate deeply with existing systems and data sources. Many shop floor applications need to interact with multiple systems, transform data, and handle complex calculations in real-time – capabilities that exceed what traditional document and form-based platforms can offer.
- The rigid nature of these platforms means they can’t accurately replicate the specific business logic and user interactions that make existing shadow IT applications valuable to workers. This often leads to simplified versions that don’t meet actual operational needs, resulting in poor adoption or the continued use of legacy applications alongside the new platform.
Workerbase’s No-Code/Low-Code Advantage
Workerbase stands apart by offering a comprehensive no-code and low-code development environment specifically designed for manufacturing applications. This unique approach enables several critical capabilities:
The platform’s no-code environment allows business users to create sophisticated applications through visual development tools. Unlike simple form builders, this environment supports complex workflow logic, dynamic data handling, and rich user interactions. This means that even intricate processes can be mapped without writing code, while maintaining the flexibility needed for manufacturing-specific requirements.
For more complex applications, Workerbase’s low-code capabilities enable developers to extend functionality through custom code when needed. This hybrid approach ensures that no application is too complex to be migrated to the platform, while still maintaining the ease of use that makes no-code development efficient.
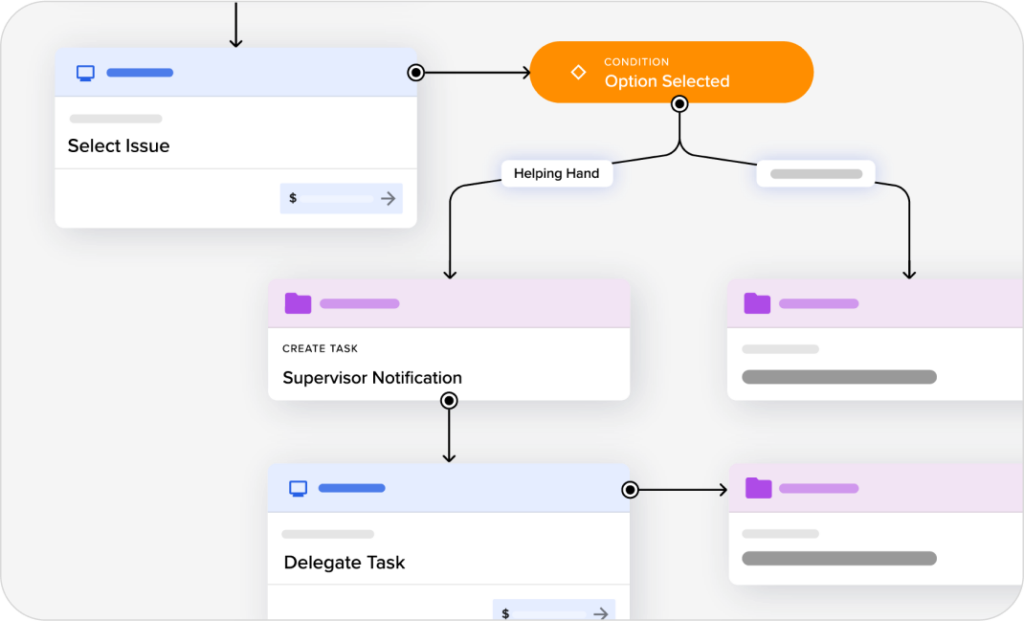
The platform’s architecture supports deep integration with existing manufacturing systems, allowing converted applications to maintain the same level of functionality as their predecessors. This includes real-time data exchange with ERP and MES systems, complex calculations and data transformations, and the ability to trigger actions in connected systems.
Most importantly, Workerbase’s approach allows for the creation of truly easy to use user interfaces that can closely match existing applications. This significantly reduces worker resistance and training needs during migration, while still bringing these applications into a managed, secure environment.
From Shadow IT to Managed Innovation
By providing a complete development environment rather than just a form builder, Workerbase enables a systematic approach to shadow IT conversion. Organizations can:
1. Accurately replicate existing application functionality without compromise
2. Enhance applications with new capabilities during migration
3. Standardize common functions across multiple applications
4. Apply consistent security and governance policies
5. Enable cross-facility sharing of best practices
6. Maintain the flexibility to adapt applications as needs change
This comprehensive approach transforms shadow IT from a liability into an asset. Instead of forcing standardization through limitation, Workerbase enables standardization through capability – providing the tools needed to bring the full spectrum of manufacturing applications into a managed environment while preserving their value to workers.
Implementation Patterns and Common Challenges
The journey to successful Connected Worker Platform implementation follows several distinct patterns, each with its own challenges and solutions. The most successful implementations typically begin in areas where existing processes cause significant pain points and where improvements can be quickly measured and demonstrated.
Building Trust and Acceptance
One of the most common challenges in Connected Worker Platform implementation is initial resistance from both IT teams and workers. IT departments often worry about losing control over applications and data governance, while workers may fear increased surveillance or disruption to their established workflows. Successful implementations address these concerns head-on through collaborative approaches to platform design and deployment.
A proven strategy is to form joint teams of IT specialists and shop floor workers during the initial implementation phase. This approach ensures that both technical requirements and practical usability needs are met. When workers see how the platform simplifies their daily tasks and gives them a voice in process improvement, initial skepticism typically transforms into active support.
Managing Legacy Systems
Another significant challenge lies in transitioning from deeply embedded legacy systems and informal solutions. Many manufacturing operations rely heavily on spreadsheets, local databases, and custom applications developed over years of operation. These tools often contain valuable process knowledge that needs to be preserved and transferred to the new platform.
Successful implementations typically include a structured knowledge capture process. This involves systematically documenting existing workflows, identifying critical data points, and ensuring that valuable process knowledge is enhanced rather than lost in the transition. The key is to demonstrate how the new platform can make this knowledge more accessible and actionable across the organization.
Regulatory Compliance and Validation
In regulated industries, such as pharmaceutical or medical device manufacturing, compliance adds another layer of complexity to Connected Worker Platform implementation. The challenge is to maintain regulatory compliance while modernizing processes. Successful implementations in these environments typically begin with a thorough validation framework that addresses both technical and regulatory requirements.
The most effective approach is to integrate compliance considerations from the start, ensuring that digital workflows meet or exceed existing compliance standards. This often results in improved compliance outcomes through better documentation, real-time monitoring, and reduced human error.
A Strategic Approach to Implementation
A successful implementation strategy typically follows four key phases:
Phase 1: Assessment and Planning (2-4 weeks)
- Review existing applications and workflows
- Identify high-impact processes for initial implementation
- Define success metrics and ROI targets
- Create stakeholder communication plan
Phase 2: Platform Implementation (4-8 weeks)
- Set up core platform infrastructure
- Configure user management and security
- Integrate with existing ERP and MES systems
- Train key users and administrators
Phase 3: Application Migration (3-6 months)
- Prioritize applications for migration
- Convert high-priority workflows to the platform
- Validate and test converted applications
- Phase out legacy solutions
Phase 4: Optimization and Scaling (Ongoing)
- Monitor and optimize implemented workflows
- Share best practices across facilities
- Implement advanced features and analytics
- Continue migration of remaining applications
Looking Ahead
The manufacturing IT landscape is evolving rapidly, and Connected Worker Platforms are becoming as essential as ERP and MES systems. Success requires more than just selecting the right platform – it demands a carefully planned implementation strategy that addresses both technical and human factors.
For manufacturing leaders, the message is clear: Connected Worker Platforms represent a crucial investment in operational excellence. The question isn’t whether to implement such a platform, but how to do it effectively. Organizations that move decisively while learning from established implementation patterns will be best positioned to capture the significant benefits these platforms offer.
The future of manufacturing lies in bringing together people, processes, and technology in a seamless digital ecosystem. Connected Worker Platforms are proving to be the crucial bridge that makes this integration possible, delivering both immediate returns and long-term strategic advantages.