What is single minute exchange of die (SMED)?
In many manufacturing environments, machines are responsible for producing multiple products. Each time a product change is needed, machine settings must be changed, which can take a significant amount of time. The Single Minute Exchange of Die (SMED) lean manufacturing methodology helps reduce these setup times to just a few minutes, improving both machine efficiency and production flexibility. By optimizing SMED and leveraging digital tools, manufacturers can greatly enhance their operations.
Benefits of single minute exchange of die
Implementing SMED offers several key advantages:
- Increased productivity: Shorter setup times allow machines to produce more parts within the same timeframe.
- Greater flexibility: Faster changeovers enable manufacturers to respond quickly to changes in demand.
- Improved line balancing: Efficient setups contribute to smoother operations for multi-product production lines.
- EPEI Implementation: SMED supports the Every Part Every Interval (EPEI) concept, facilitating lean production strategies.
Structured approach for conducting a single minute exchange of die analysis
Conducting a Single Minute Exchange of Die (SMED) analysis follows a structured methodology to systematically identify inefficiencies in the changeover process and reduce setup times. When the method was first developed by Shiego Shingo, it had 8 fundamental techniques that should be considered, these have been modernized into a new 8 stage step-by-step approach:
1. Observe and document the current changeover process
- Conduct a time study by recording the entire changeover process.
- Break down each step and classify them as internal (requiring the machine to stop) or external (can be done while the machine is running).
- Use video analysis or real-time monitoring tools to capture inefficiencies.
2. Separate internal and external setup operations
- Identify tasks that must be completed when the machine is stopped (internal setup).
- Identify tasks that can be performed while the machine continues running (external setup).
- Document setup steps using standardized formats such as checklists or digital work instructions. Workerbase’s digital work instructions ensure consistency and reduce errors.
3. Convert internal setup to external setup
- Shift as many internal setup tasks as possible to external setup.
- Ensure necessary tools, parts, and materials are pre-staged and ready before the machine stops.
- Utilize digital work coordination to notify operators when external setups should start.
4. Optimize internal setup operations
- Standardize adjustments by using fixed positioning mechanisms or quick-change fixtures.
- Use quick-fastening methods such as clamps instead of bolts.
- Reduce motion waste by optimizing the layout and accessibility of tools.
- Introduce automation where applicable (e.g., servo-driven adjustments instead of manual settings).
5. Streamline external setup tasks
- Organize shadow boards for tools and ensure required materials are within easy reach.
- Pre-assemble and pre-align components to reduce adjustment time.
- Automate external setup tracking with digital workflow management tools.
6. Implement parallel operations
- Assign multiple operators to execute setup tasks simultaneously.
- Optimize workforce scheduling to reduce idle time during setup.
- Use real-time digital coordination tools to track and allocate tasks efficiently.
7. Validate and standardize the optimized setup process
- Conduct multiple trials to ensure consistency in the new changeover process.
- Develop standardized digital work instructions with step-by-step guidance.
- Implement training programs for operators to ensure adherence to the optimized process.
8. Measure, analyze, and continuously improve
- Track setup times using real-time monitoring tools and digital dashboards.
- Use a setup matrix to analyze the efficiency of different product transitions.
- Implement AI-driven insights to further refine and optimize setup sequences over time.
This structured approach, when combined with digital work instructions, real-time coordination, and AI-driven analytics, ensures that setup times are minimized and efficiency gains are sustained.
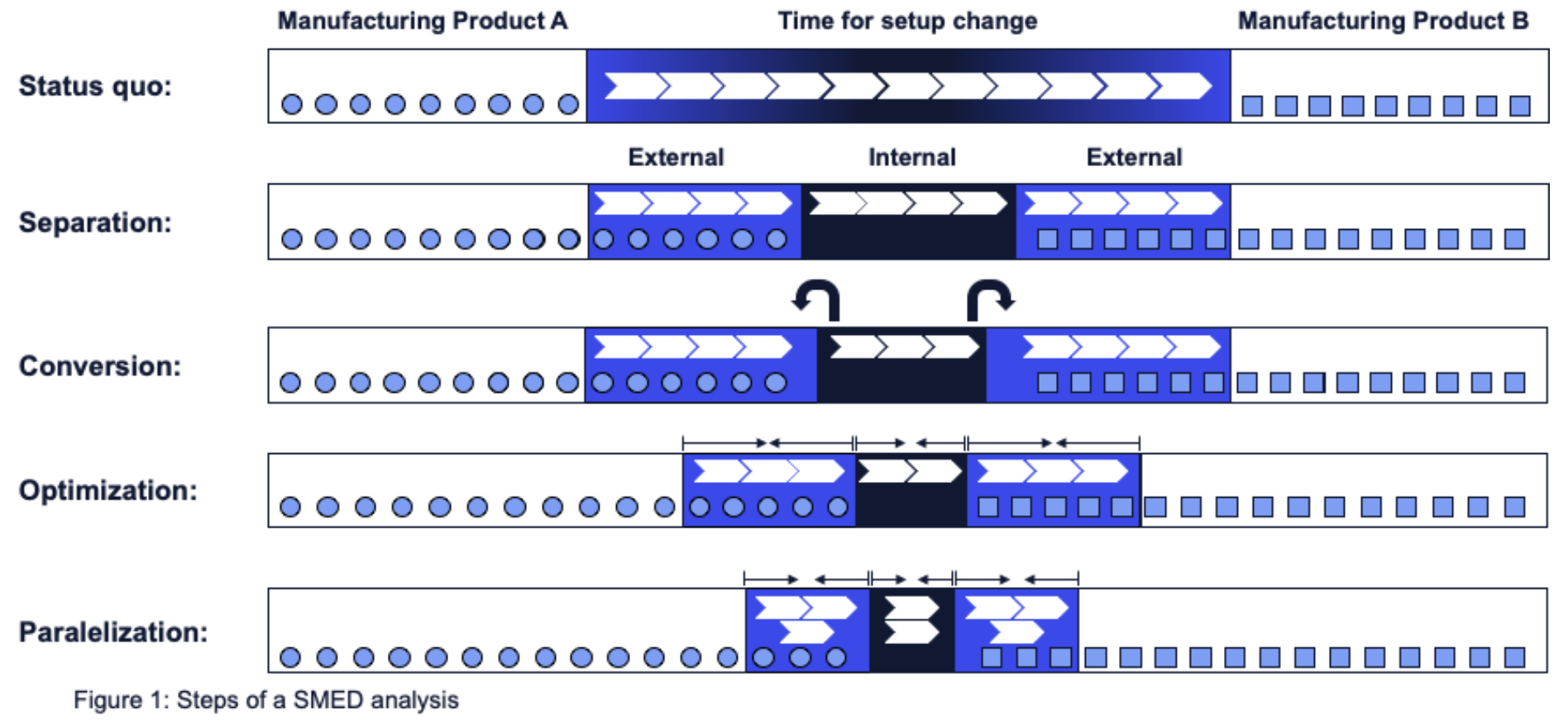
The role of a setup matrix in SMED
A setup matrix helps measure and optimize setup times between different product changes. By tracking these times, manufacturers can:
- Identify bottlenecks and streamline machine changeovers.
- Optimize model sequencing based on the shortest possible setup transitions.
- Implement EPEI strategies to balance production schedules efficiently.
Example of a setup matrix
A setup matrix records the transition times between different product setups on a machine. Below is an example matrix for five different products (A, B, C, D, E):
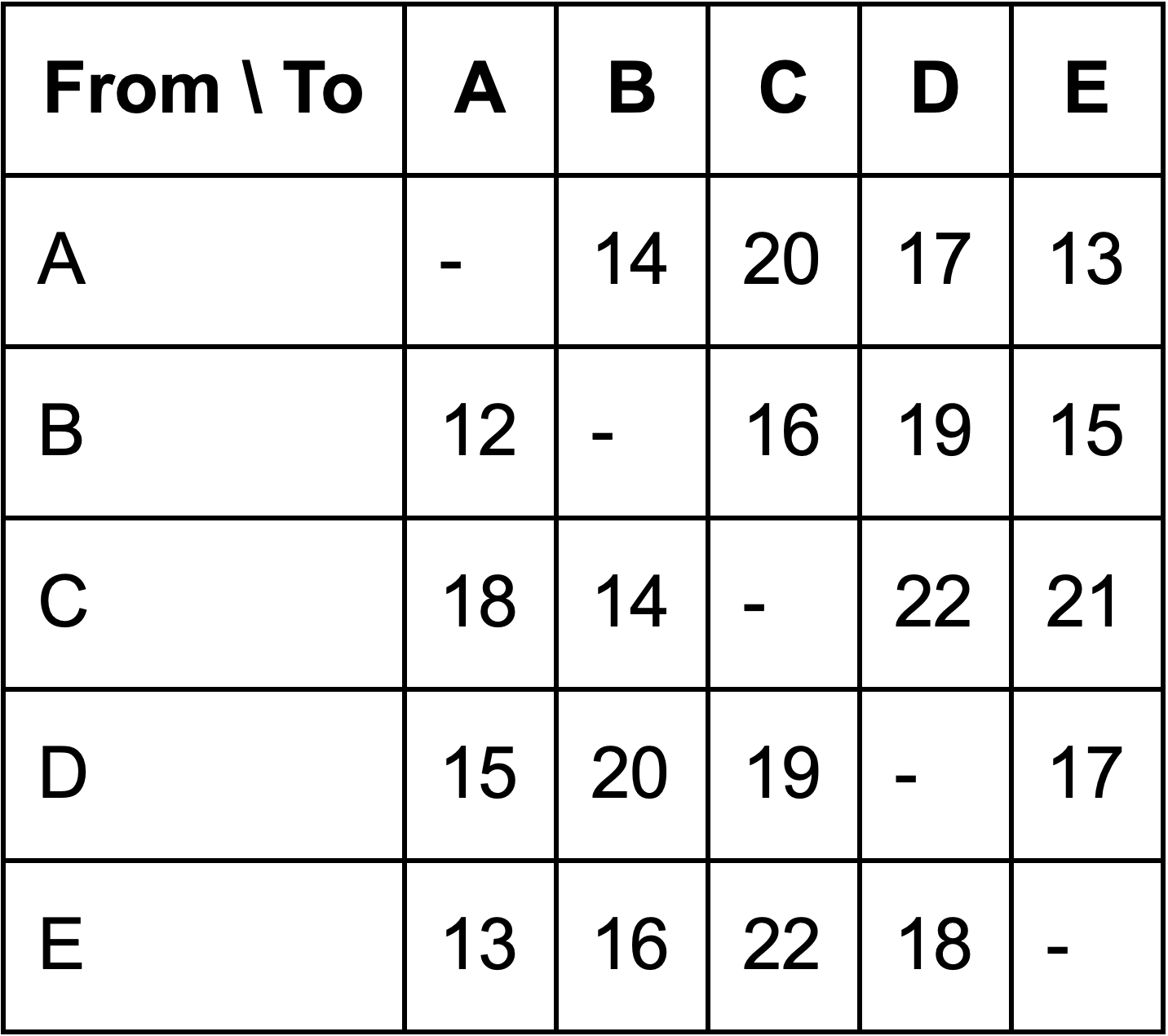
Using this matrix, manufacturers can determine the best sequence to minimize downtime.
For instance, the optimal order might be A → E → B → C → D, based on the shortest total transition time. Digital tools like Workerbase can automate setup matrix tracking, conduct analysis of historical data, and recommend the most efficient production sequence in real time.
How to improve single minute exchange of die with digital tools
Digital work instructions
Modern manufacturing setups involve a complex array of parameters that operators must adjust quickly and accurately. Digital work instructions provide step-by-step guidance, ensuring operators follow the optimal sequence for the fastest setup. This is particularly beneficial in complex changeovers where efficiency gains are most significant.
Digital work coordination and task prioritization
Digital work coordination tools assign setup tasks based on operator skills and prioritization. These tools:
- Distribute tasks dynamically based on urgency.
- Enable real-time monitoring of setup durations.
- Aggregate anonymized data for continuous improvement.
AI-Driven setup optimization
With real-time and historical data, manufacturers can generate dynamic setup matrices for each machine. AI-driven algorithms analyze past setups to recommend optimized model sequences, significantly improving overall production efficiency.
Key benefits of digital tools for single minute exchange of die (SMED)
The aforementioned digital tools are all possible with Workerbase’s Connected Worker Platform and enhance SMED implementation by offering the following advantages:
- Faster and more accurate setups with guided work instructions delivered via mobile and wearable devices.
- Reduced downtime by coordinating external setups proactively through Workerbase’s digital workflow automation.
- Continuous improvement with real-time data tracking and AI-driven insights from an analytics platform.
- Enhanced workforce efficiency through smart task distribution, ensuring the right operators handle setup tasks at the right time.
Conclusion
Digitizing SMED transforms traditional manufacturing setups into highly efficient, flexible production lines. By integrating digital work instructions, real-time coordination, and AI-driven insights, manufacturers can significantly reduce changeover times, optimize production sequences, and boost overall operational efficiency. Workerbase’s Connected Worker Platform makes these digital SMED tools easy to implement, ensuring lean manufacturing and maintaining a competitive edge in today’s fast-paced production environment.